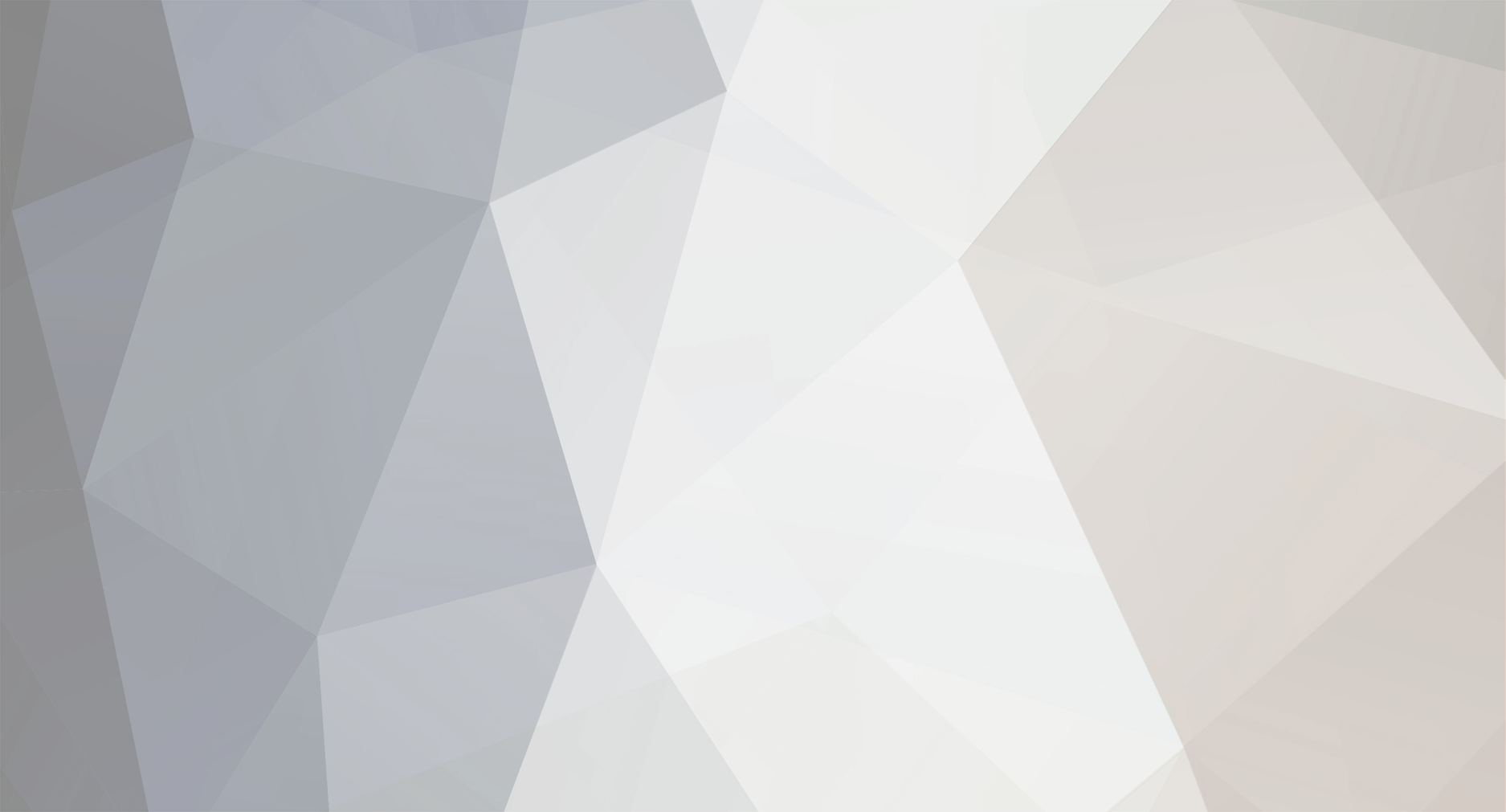
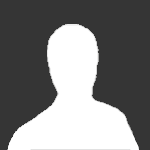
Toppless72
-
Posts
195 -
Joined
-
Last visited
Content Type
Profiles
Articles
Forums
Gallery
Events
Posts posted by Toppless72
-
-
The roll pin at the bottom of the distributor shaft that holds the gear on the shaft may be broken or sheared off. Pop the cap off and see if the rotor turns while someone cranks it. If not, that's where I would start.
Good luck
-
Willie,
The 1972 Assembly manual does not show the bracket you have here. It only shows the large brass wire loop connected to the wire harness and attached at the headlight switch. I'm not sure where it would go if it is a 1972 part.
-
There are 3 lengths of the THM350. Over all lengths are:
27 11/16 inches
30 11/16 inches
33 27/32 inches
The first gen M/C uses the 27 11/16" case and tail assembly. At this point the cheapest way out would be shorten the drive shaft. However, I'm not sure of the impact of using the 9" tail shaft would be or what other modifications are necessary.
Maybe some of the other members that have been down this road will comment.
-
WOW! At the big end your hood has some serious air too. It raised up 3 inches.
-
Jared,
Stomping it to the floor too much will have that effect also.
-
6264828 is the part number for the jacking instructions for a 1972 according to the assembly manual. What is subject of the caution label you're looking at?
-
I'd try Leo or Jared on the board here. I'm sure they would have several.
-
The piece under the passenger’s seat is a simple switch. The weight of a person sitting on the seat flexes the plastic strap allowing the two strips of metal to contact each other completing the circuit. By connecting the seat belt it breaks the ground circuit for the buzzer shutting it off.
During your test:
1. Was your door open? This will cause it to buzz as well.
2. Was there a person on the passenger side? If not it would not have affected your test. If so, did they have the belt on?
3. Did you have the driver’s side belt on? There is no switch on the driver’s side. The theory is that if the engine is running and the car is in drive, there will be a person in the diver's seat. Therefore, no switch is necessary. If the car is running in drive and no one is in the diver's seat you have bigger things to worry about than a buzzer.
4. Has something happened to the retractor on the driver’s side? Both retractors can supply the ground necessary to complete the circuit. You may want to check your side as well.
5. Lastly, you can also try un-plugging the connector on the neutral start switch on the column down by your brake pedal. It will have a yellow wire with a black stripe and a black wire.
One more thing... This is a safety device that was installed to help keep you safe. You should make all efforts to insure it’s in good working order to protect yourself and your passengers as soon as possible.
-
It is a white plastic and matal strap located within the springs below the front seat passenger. To remove it, you will have to take the seat bolts/nuts loose and tip the seat back to get under there. You may opt to just unplug it and leave it there until you repair the retactor. The two wire plug runs up from a split in the carpet on the right side.
-
I hear you Doug and here is the thing I don't get. I was in the automotive parts manufacturing business for 25 years. It cost the same to engineer and manufacture a bad part as it does to engineer and manufacture one that works well. So why can't they get it right?
-
This is not a good option. It's mainly used on Demolition derby cars. You will strip or break axels continuously. I’d look for a good aftermarket Posi unit.
-
A pair of needle nose pliers opened up, one tip in each hole and turn. Works for me.
-
I know this sounds like nit-picking but you don’t have or need a temperature sensor. A temperature sensor works within a computer controlled closed loop system and sends varying voltages to the computer based on changes to the temperature of the engine coolant. This allows the computer to make changes to fuel trim to compensate for atmospheric conditions IE: heat cold etc.
The system in these cars requires a temperature sending unit. If you have warning lamps, the sending unit has a metallic contact that expands while the engine warms. Once it reaches a set point in length due to heat it makes contact to ground and lights the tale-tail lamp on the dash. A sending unit for warning lamps is either off or on. There is no in-between. In order for the system to work correctly you’ll need a high quality temperature sending unit.
-
My '72 has A/C but it doesn't have one either.
-
My '70 Chevelle was one that was ordered with the strangest group of options.
1970 Malibu Convertible
307 Cu.In 2 barrel - 3 speed on the column
Air Conditioning
AM - FM - Mono radio
Power door locks (convertible?)
Bucket seats no console
power trunk
Rear mount ant.
Lighting group
and full disc hubcaps - no special wheels
It just seemed odd to me that it had the 307 - 3 speed on the column with the rest of the options that were ordered.
-
Dis-connect the wire going to it or remove the belt. If the motor is running and it's not charging the light should come on.
-
Ian,
If you think it would be beneficial to others it’s fine with me. Feel free to edit it as you see fit as I tend to get too wordy at times.
JC
-
Windshield wiper motor testing.
The issue of windshield wiper failure or testing has come up here from time to time. The way the switch works and supplies power has been a bit of an enigma to many including me. I’ve been studying this system and thought I would post my findings.
Well, the switch supplies no power to the motor. So we’ll start there.
First, how to test your W/S wiper motor on the car.
If you have windshield washers your motor will have two harness plugs going to it. For now, we’ll be concentrating on the 3 wire motor plug. Fig.1
Step one as always; insure your W/S wiper fuse is good before performing any further tests.
Turn the key to the run position and leave the W/S wiper switch in the off position.
Using a grounded test light at the 3 wire motor plug, insure you have power to the middle wire # 2. This wire is energized when the key is in the on position and is hot at all times while the key is on. If you do not have power here with the key in the on position, trace back all connections to the fuse box. This wire does not go to the W/S wiper switch.
Remove the connector from the motor. (IMPORTANT: make the test connections in this order)
Hook a good chassis ground to connectors # 1 and # 3 on the motor.
Hook a jumper supplying 12 volts from the battery to number 2 on the motor. Take care not to ground your 12 volt power source to the other connectors or to the motor housing
At this point your motor should be running at the slow speed.
Remove the ground wire going to # 3. The motor should run in high speed.
Replace the ground to # 3 connector. The motor should return to slow speed again.
As it’s running in slow speed, remove the ground to the # 1 connector. The motor should move to the park position.
If your motor fails any of these tests you have an issue with the motor and further testing on the motor or replacement is necessary.
Next, testing your wiring at the motor.
We have tested the power circuit earlier so on to the ground circuit. All these tests should be conducted with the key off.
Place the key and W/S wiper switch in the off position.
Using a test light connected to the battery; probe wire # 1. The wire should be open. If you get a ground you most likely have a short to ground along the harness or a faulty switch.
Using a test light connected to the battery; probe wire # 3. The wire should be grounded. If you do not get a ground, you have a broken wire, a faulty switch, or the switch is not grounded properly.
Place the W/S wiper switch in the low speed position.
Using a test light connected to the battery; probe wire #1 & # 3. The wires should both be grounded. If you do not get a ground at both wires, you have a broken wire, a faulty switch, or the switch is not grounded properly.
Move the W/S wiper switch to high speed.
Using a test light connected to the battery; probe wire # 1. It should be grounded. If you do not get a ground, you have a broken wire, a faulty switch, or the switch is not grounded properly.
This test should be conducted with the key on and the connector attached to the motor.
While the W/S wiper switch is still in the high position probe wire #3. It should show a very small amount of power. Your test lamp should be very dim. If you use a VOM to conduct this test you’ll find it has about 3.25 volts. This is the ground signal needed by the electromagnet used to activate the parking pawl after you move the switch to the off position. If there is no power on this wire, the internal resister at the connector is bad or not making contact with the motor case.
Testing the W/S wiper switch
All of the references to the three connectors coming out of the switch will be made viewing it from the back side, in-car-position. The connector on the right connects to terminal # 1 on the S/W wiper motor. The connector in the middle of the switch connects to terminal # 3 on the W/S wiper motor and, the connector on the left connects to the ground side of the two wire connector for the W/S washer.
Remove the wire harness plug.
Using a test light connected to a 12 volt source probe all 3 connectors starting on the right. This should be your results.
Switch position Connector #1 Right Connector #2 Midd. Connector # 3 Left
Off position # 1 Open # 2 Grounded # 3 Open
Low position # 1 Grounded # 2 Grounded # 3 Open
High position # 1 Grounded # 2 Open # 3 Open
Depressed washer button
#1 Grounded # 2 Grounded # 3 Grounded while holding the button in only.
If any of these tests fail, insure the metal switch mounting bracket is securely contacting ground and re-test. If the second test fails suspect a faulty switch.
Next, testing the W/S washer wiring.
As from the earlier power tests, you should have power to one side of the 2 wire connection as soon as the key is turned to the run position.
While testing the ground side you will need a helper or you’ll have to place your test light so that it can be seen from inside the car.
Using a test light connected to the battery; probe the black wire at the two wire connector. When W/S washer button is depressed; you should have a ground. When released there should be no ground.
If ground is constant, the W/S wiper switch is faulty or the wire is shorted to ground. A constant ground to this wire will cause the W/S washer pump to function when ever the key and W/S wiper switch is on.
This information is based on the 1972 model and I'm just assuming the 1970 and 1971 would be similar.
-
Charlie,
Here are some tips that may help.
Before installing it, take the locking pin and slide it into its bore in the upper bowl. Make sure it slides smoothly and does not bind at all. It should slide all the way through in both directions without any rough spots. Smooth out any rough spots using emery cloth or sandpaper on the pin and in the bore.
Once the locking pin is in its bore in the bearing housing, hold the locking pin spring nearly upside down hook it around the pin in the groove and rotate it down capturing the sector gear with the spring loop. Then, continue to bring it down to its rest position where you can install the screw.
Next, be sure to put some grease in the locking pin bore before you assemble the upper bowl.
If you're still having trouble fitting the upper bowl try installing it without the locking pin to see if it's binding elsewhere. Correct any other causes preventing the bowl to seat properly.
Now, work instructions... When I was a senior manager of manufacturing for an OEM automotive supplier, one of my responsibilities was to approve every work instruction placed on the manufacturing floor. My directive to my manufacturing management team was that, when writing a work instruction, anyone should be able to take that instruction sheet and perform the task it outlines. That led to me editing many of them and rewriting more than a few.
Get back to us and let us know how it’s going.
JC
-
Charlie,
If I understand your description, unfortunately, you've gotten a little ahead of yourself.
Once you get the bearing housing on and the pivot pins installed your now ready to install the locking pin, locking pin spring, ignition rack, sector gear, and sector gear snap ring. All of these go on before you install the turn signal housing (What I call the upper bowl).
Slide the locking pin into its bore with the flat side facing down.
Slide the sector gear onto the lock cylinder rod lining it up with the ignition rack.
Insure the rotation will align the large tooth on the gear with the proper position on the rack.
Install the snap ring.
Loop the hook of the lock rod spring into the groove at the lower end of the lock rod.
Rotate the lock rod spring's long end to the rest position and install the screw to hold it in place. (Take care to insure the loop of the spring that extends into the sector gear is in the proper position.)
Rotating the lock cylinder rod to the run position will withdraw the lock pin into the bearing housing to its shortest position.
Align the upper bowl over the bearing housing and start pushing it down.
Assure the lock pin is entering its bore as you slide it down.
Once it's seated you can install the 3 screws.
Try that and let us know how you're doing.
JC
-
As I understand it, the painted sport mirror was a left side only unit. There never was a painted right side sport mirror for a first gen M/C.
Maybe others can chime in on this to confirm.
JC
-
Charlie,
It sounds like you're becoming a first class column expert. LOL
The switch provides all the detent positioning for the ignition rod and rack movement. Therefore, the only position that's critical at the lock cylinder is the lock position. This is so you can get the key out.
Place the switch in the second detent position opposite of the start position. Place the lock cylinder in the lock position. Mount the switch to the column and leave the bolts for it loose so that it will slide up and down as you rotate the lock cylinder. Center the lock cylinder in the lock position.
Tighten the bolts to the switch until they hold the switch in place. Rotate the key to the start position to insure you are reaching the spring back point. Rotate the key back to the lock position. Press in slightly and turn it to the accessory position. Make fine tune adjustments with the switch until all positions are reached.
Adjusting the switch is one of the last parts of the operation so you'll need to be at a point where you can hook up the battery power to insure you're making contact with the starting circuit when you're adjusting the position of the switch.
JC
-
Charlie,
Never did the '06 Impala job. Once I cleared the code which turned the MIL off he said, "Well, It looks like you fixed it". I told him it would most likely come back on but he's put about 300 miles on it since then and no light so far. I guess we'll see.
It takes a special socket to tighten those bearing housing support screws. You can buy one or do as I did and modify one to fit with a grinder. Your other option is to use a quarter inch drive/6MM socket. It also works well.
Good luck and let us know how your doing.
JC
-
Yep, P2070 IMT valve "stuck open". I found the part at a GM parts warehouse for $71.00. I guess I'll be tearing off the power steering pump to get to the valve Saturday morning.
Later,
JC
Wiring Diagram
in Electrical Tech
Posted
I'm not too good at creating links but if it works, I believe this will help you.
1971_chevelle_wiring
It takes a minute to load but its worth the wait.